This article is part of SNAP’s Digital Transformation series. Building on the earlier feature on Data Science and AI (DSAI), it explores how iROC is driving real-time operations, smarter dispatch, and greater system resilience.
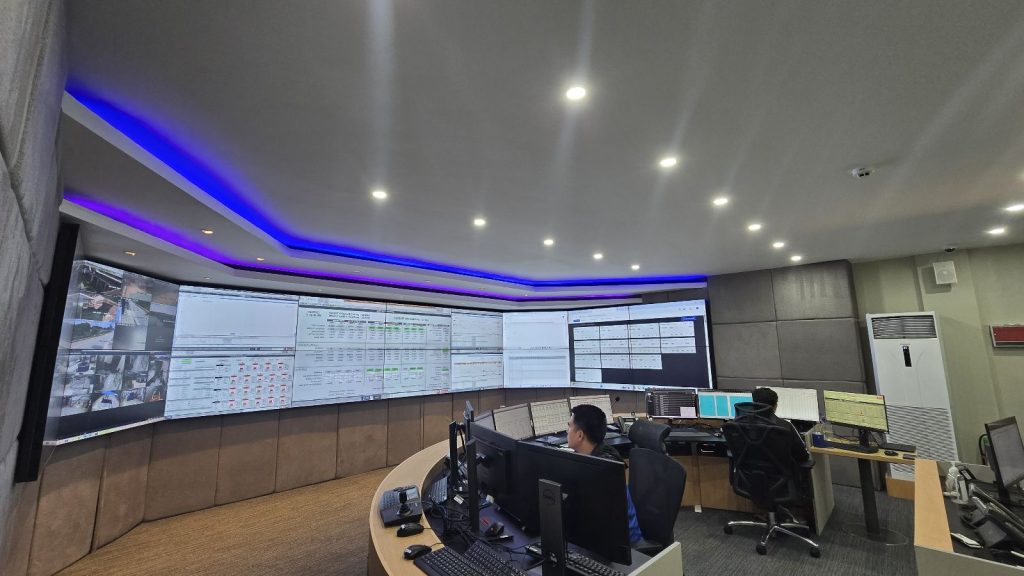
In 2020, SN Aboitiz Power (SNAP) made a bold move: instead of outsourcing digital transformation, it bet on its own people and empowered them through the Data Science Upskilling Program (DSUP). Domain experts became citizen data scientists, and a belief took root: transformation works best when it starts from within.
Today, that belief powers iROC—the Integrated Remote Operations Center, SNAP’s most ambitious systems reinvention yet. If DSUP makes data science accessible, iROC makes it operational. It’s the next chapter in SNAP’s digital journey, bringing together talent, technology, and insight to create smarter, scalable operations for a renewable future.
“We began remote operations in Benguet eight years ago, and since then, we have continuously improved our processes. iROC is a natural next step. As digitalization, automation, and connectivity become increasingly important in our industry, iROC allows us to process data more efficiently and accurately, which then allows us to make informed decisions more quickly, and to generate insights that can drive innovation and growth,” said Melvin Catu, SNAP’s Chief Technology Officer and Executive Officer of the iROC project.
Transforming for a Renewable Future
With a 1,400MW growth target by 2030, SNAP needed more than incremental change – it needed an operational platform that could scale. In designing iROC, SNAP aimed to create a future-ready hub that could centralize and streamline operations across its renewable assets. It was shaped by global benchmarking, drawing lessons from international partners, internal experience with SNAP’s own Network Operations Center, and the rise of digital tools.
The answer wasn’t to add more layers, but to rethink the system entirely. That meant moving away from siloed, site-specific operations and towards a model where people, processes, and data could work in sync—regardless of location.
As SNAP’s Chief Information Officer Maria Theresa “Mitch” Cabigon emphasized, “This is more than a technology initiative. It’s about building a best-in-class organization—where our people, systems, and strategy come together to lead the way.”
Upskilled People in Action: iROC’s AI-Ready Workforce
iROC’s success would not have been possible without the foundation laid by DSUP. The program gave team members the digital fluency to contribute to the initiative’s technical structure.
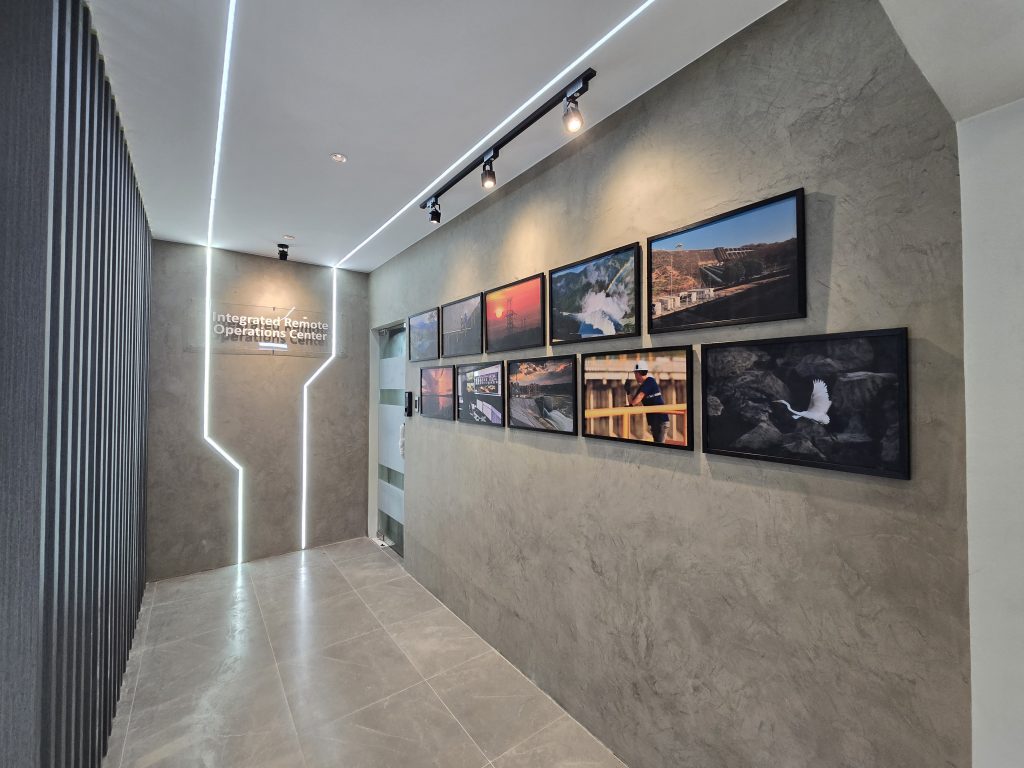
On the technology side, teams had to stitch together data and controls across geographically dispersed hydro plants—requiring robust connectivity, a reliable data warehouse, and an interoperable automation platform. From Auto-Dispatch logic to SCADA integration and CIS, no system was left untouched.
As Data Management and Cloud Operations Head Efren Doren explained, “There are still minor challenges—especially in data wrangling—but that’s the nature of transformation. What matters is we now have the tools and internal capability to keep improving the data pipelines ourselves.”
But the deeper challenge was human. Merging teams, redefining roles, and managing relocation all required deep change management. SNAP responded with site immersions, FGDs, team buildings, and open dialogue. People were trained, involved, and empowered—not just to accept the shift, but to lead it.
Launching a Smarter and Faster Future for SNAP
On February 20, iROC officially launched into full operations. One of the most pioneering aspects was SNAP’s in-house development of five-minute auto dispatch functionality – one that automates energy and reserve dispatch across multiple power generation units in real time. This positioned SNAP as a leading provider of ancillary services, helping to stabilize grid frequency every five minutes.
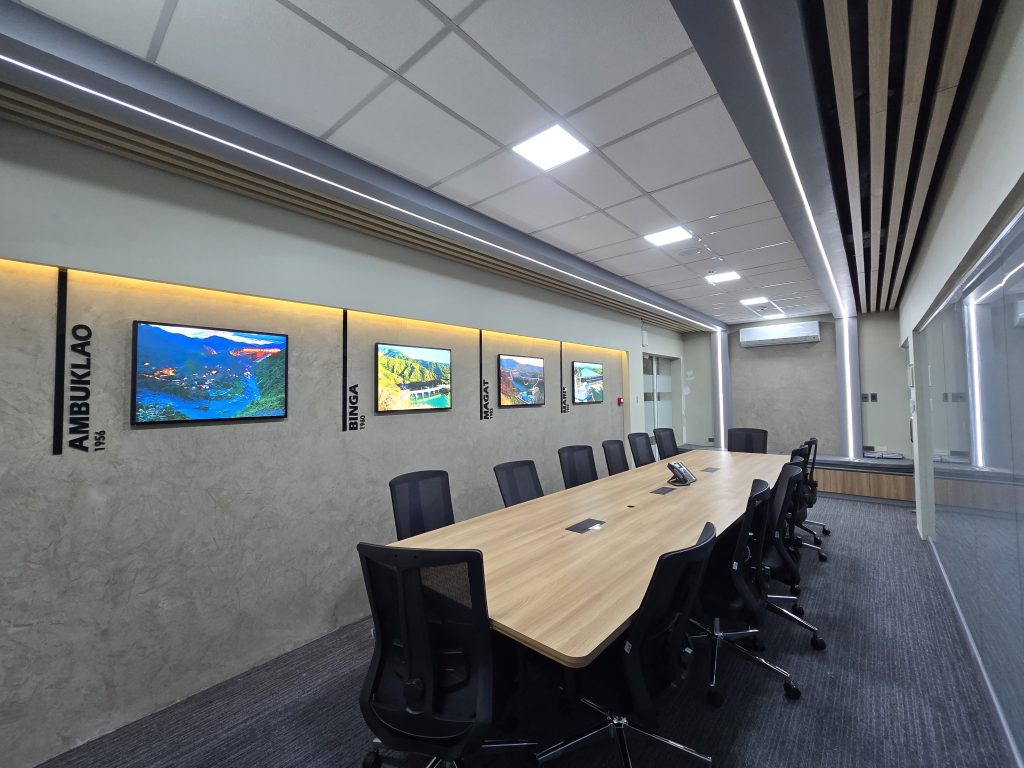
As AVP Plant Manager Homer Ramos shared, “the goal was to build a system that could handle our growth with speed and resilience. iROC isn’t just a control center—it’s our response to what the future demands from us as an energy company”.
With visibility across sites, planning, maintenance, and regulatory reporting became smarter and faster. By eliminating the need for a duplicate control room, iROC also improved capital efficiency and boosted Internal Rare of Return for future projects.
What iROC Means For SNAP’s Future
iROC didn’t just change how SNAP operates—it changed how teams work. Manual updates have been replaced by synchronized, real-time data, making plant coordination more agile and responsive. Operators now learn from other sites, while planners and traders access consolidated insights for quicker, sharper decisions.
As Head of Integrated Remote Operations Center Ariel Yao shared, “This isn’t just about centralizing systems—it’s about centralizing learning. With iROC, our teams get visibility into how other plants operate. That’s how innovation spreads faster.”
As a system, iROC is designed to evolve. With a Digital Twin initiative now also underway, SNAP is shifting from reactive to predictive operations—anticipating issues before they arise, optimizing maintenance, and supporting regulatory compliance through automation. These steps are part of its broader ambition to build best-in-class operations that are not only future-ready, but future-defining.
But iROC is also a reflection of who SNAP is becoming. If DSUP showed what happens when you empower people with data, iROC shows what’s possible when they actually use that data to run the business better. It’s a move from siloed to integrated, from reactive to forward-looking.
“These initiatives reflect our commitment to providing innovative and sustainable energy solutions,” said Joseph Yu, President and CEO of SNAP. “with the launch of our integrated remote operations center, we are enhancing energy security and grid stability, in line with our long-term sustainability goals.”
SNAP isn’t just adopting technology—its building culture around it. Transformation here isn’t a one-time shift, but a way of working. So ask yourself – what could you automate, integrate, or improve with the tools now at your fingertips?